Recently, the whole equipment has been successfully produced and delivered on time. It is the largest diameter, the largest tonnage, the highest quality requirements and the most difficult welding equipment since the metalworking workshop of JNG manufacturing base has been established.
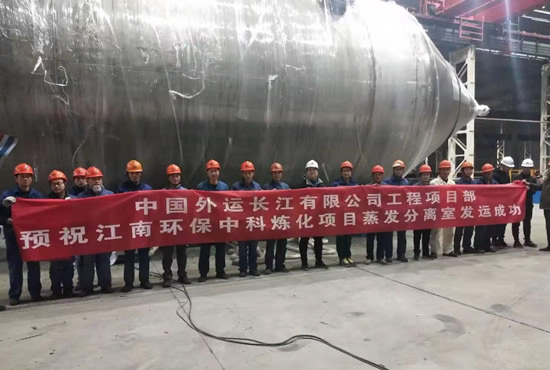
Picture 1 Production and delivery of ZhongKe project evaporation separation chamber
The evaporation separation chamber of Zhongke Refining and Chemical project has a diameter of more than 5.3 meters and a length of 16 meters. The material of the upper section is s31603, and the material of the lower cone section is 2507. The weight of the entire equipment is more than 50 tons.
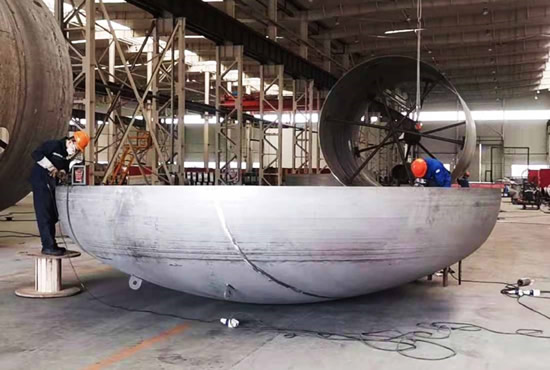
Picture 2 Elliptical Head with Diameter of 5.3 meters
The welding of super duplex stainless steel and the transportation are two of most difficult parts. In order to improve the welding efficiency and the production quality, the automatic welding technology is applied in the evaporation separation chamber. The welding seam of automatic welding technology has good appearance and uniform width. This technology initially has been initially applied in the production by JNG. The appearance and internal quality met the requirements of national technical standards. Although it is the first time for a JNG to use automatic welding, the one-time pass rate of radiographic testing is more than 99%, which not only reduces the cost, but also improves the production efficiency and ensures the delivery time. Mr. Cai, the Dean of the EPC contractor, Zhenhai Refining and Chemical Design Institute, and Mr. Li, senior engineer, the expert of equipment manufacturing, fully affirmed JNG’s equipment manufacturing quality by supervising and inspecting the product quality and inspection process.
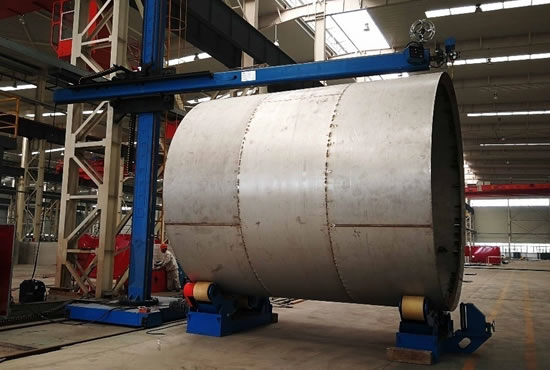
Picture 3 Full application of automatic welding and submerged arc welding
According to past delivery experience and plan offered by logistics company, the maximum transportable diameter of land transportation is 4.5m. Thus, the original production plan of the evaporation separation chamber was to transport the different pieces of it to the rental site of the dock to complete the final assembly. In this plan, the rental company's quotation was quite high. Our company required the manufacturing center to make full use of the existing equipment to optimize different parts of the transportation plan, transform existing equipment, make special tools and try to purchase as few new equipment as possible. We arranged related personnel to cooperate with logistics company and done multiple filed trips. Through comparison, we decided to produce the equipment at our manufacturing center instead of outsourced processing and this saved almost half of the cost.
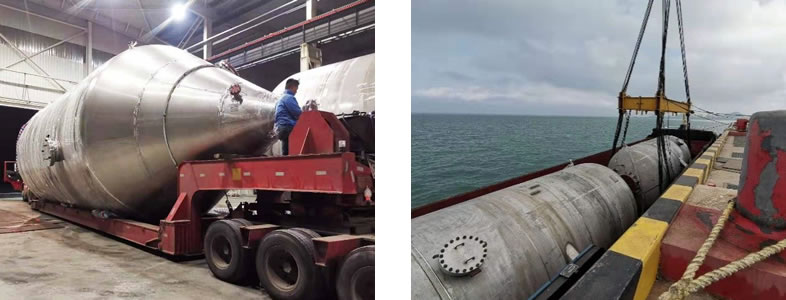
Picture 4 Combination of land and sea transportation
The evaporation separation chamber is the first complete large-scale equipment that is produced, manufactured and inspected strictly in accordance with the pressure vessel standard by our manufacturing center. After the product is completed, the entire acid pickling passivation, water pressure test and nitrogen-filled sealing protection treatment are performed according to the standard. After inspection by the owner and Zhenhai Institute, the two equipment fully met the requirements of the pressure vessel and was accepted. The success of the production and delivery of this equipment by our manufacturing center fully proves that we have full manufacturing and transportation capabilities of large pressure vessels and have mastered the entire manufacturing process of ultra-low carbon stainless steel and super duplex stainless steel. All these technology lays a solid foundation for the second rapid growth of our company. |